La problemática que ha traído consigo la guerra de Ucrania, el repunte en los casos de Covid-19 en el mundo y una necesidad por recuperar el terreno perdido por la pandemia está provocando una necesidad de aumentar la producción sin dejar de lado la seguridad de los empleados y mantener las cadenas sumisas activas, por lo que el uso de la robótica colaborativa se posiciona como la opción más viable dentro de las empresas.
La automatización de los procesos se perfila como el futuro dentro de la cadena de producción de las empresas ya que a con ella se están sustituyendo y/o reemplazando tareas que han sido designadas a robots colaborativos. Específicamente, se trata de actividades que son repetitivas, tediosas, peligrosas o sucias, por lo que también suponen un plan a futuro sobre seguridad.
Es fundamental que las industrias desarrollen tecnologías que sean más intuitivas, en donde se pueda colaborar más y exista esa sinergia entre el hombre y la máquina. Estos nuevos paradigmas se han visto reflejados dentro de la industria 4.0 y sentaron las bases de la industria 5.0, a la 5ta Revolución Industrial, donde ya se habla de una colaboración real entre hombres y robots.
Te puede interesar: Robots podrían sustituir a chefs humanos al preparar alimentos
La evolución de la robótica tradicional a la robótica colaborativa
Dentro de las industrias, el concepto de la robótica ha ido cambiando y evolucionado de manera constante; el concepto de la robótica tradicional ha desembocado en lo que ahora se conoce como la robótica colaborativa. Anteriormente, los primeros robots estaban diseñados con grandes engranes, daban muy alta productividad y generaban un alto rendimiento pero necesitan lubricación y mantenimiento, por lo que no eran seguros.
Por otro lado, los Cobots o robots colaborativos usan motores más pequeños y pueden ser más compactos. Sin embargo, este tipo de robótica tiene un mayor costo que está en la seguridad a la hora de buscar la integración. Además, no requieren una lubricación como los robots y el mantenimiento preventivo es relativamente más sencillo.
Cabe resaltar que esta nueva generación de robots puede tener una instalación rápida; además de que son más fáciles de programar, se puede mover de un lugar a otro en diferentes aplicaciones, no necesita mucho espacio y colabora hombro con hombro con las personas y tiene un rol bastante eficiente.
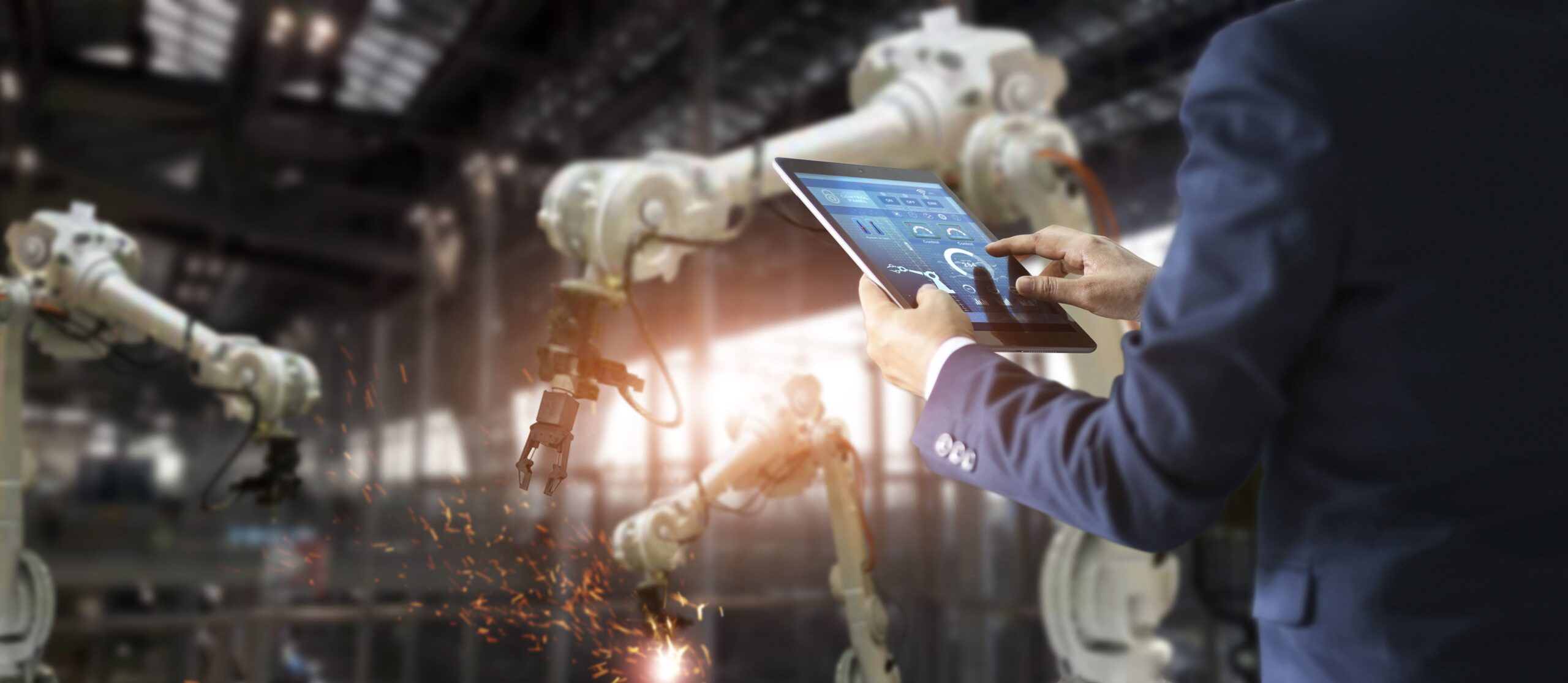
La resistencia a la implementación de robots
Dentro del webinar: ¿Cómo empezar a Automatizar con Cobots?, Jesús Coronado, encargado de la zona noreste para el canal de distribución para Universal Robots, explicó que “las empresas que se resistieron a los cambios en la robotización generalmente impulsada por la creencia de la reducción de empleos tuvieron una tendencia de éxito a la baja”.
Por otro lado, las empresas que implementaron la robotización en su cadena de suministro tuvieron un crecimiento a lo largo de los años, ya que desarrollaron posiciones más técnicas que sumaran mayor valor a la empresa y eso se traduce en un en un crecimiento como tal, continuó.
“El automatizar procesos se ha convertido en una necesidad por la falta de personal para mantener una operación consistente; además, se ha comprobado que la implementación de robots podría aumentar la productividad, así como la competitividad de los productos que se desarrollen ante la constante y cambiante demanda de los consumidores” concluyó Coronado.
Te puede interesar: Robots colaborativos para un paletizado más seguro