El pensamiento del filósofo Bertrand Russell, “Todo conocimiento humano es incierto, inexacto y parcial”, nos coloca en la posición de preguntarnos ¿estoy basando mis acciones y decisiones en la ejecución logística sobre conocimiento o anécdotas? ¿lo realizo por intuición o solo siguiendo una tradición o intuición?
Las interrogantes no solo son desafiantes, sino que más allá nos lleva a revisar los elementos y aspectos bajo los cuales tomamos decisiones.
En el caso de los niveles de inventario, lo anecdótico ocasiona distorsiones que derivan bien sea en excesos o defectos en disponibilidad de stock.
Ahora bien, el empleo de la formula estándar para calcular una primera aproximación de cuál podría ser el nivel de mínimo (Safety Stock o SS) y allí determinar los valores máximos – permisibles – y el punto de reabastecimiento, sigue siendo totalmente valedera.
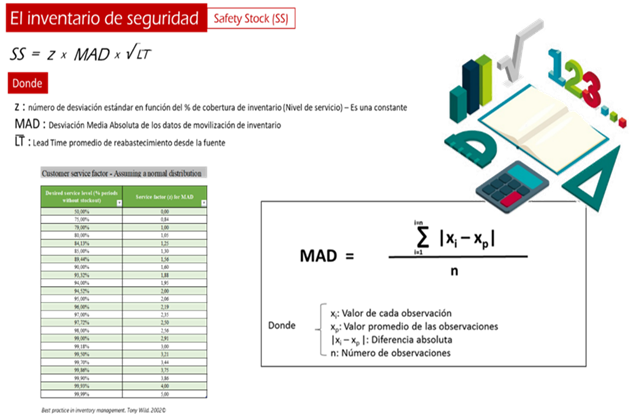
Su aplicación, como ya mencionamos, es estándar. ¿Dónde se ubicaría la diferencia al momento de utilizarla en la industria de los alimentos? En las consideraciones de atributo arbitrario que se tienen que asumir. En primer lugar, el nivel de cobertura. ¿Un 95% sería factible?
La respuesta está íntimamente relacionada con la capacidad de almacenamiento y las condiciones de fiel cumplimiento.
Por ejemplo, es un material susceptible a la degradación por efecto de la temperatura, alta o baja; es un producto que no puede estar más de cierta cantidad de tiempo en contacto con el aire, es un material que no se puede colocar directamente a la superficie del almacén o bodega.
Este porcentaje de cobertura, en función del uso no estaría reñido con la fecha de caducidad. Se debe almacenar aislado de otros para evitar contaminación cruzada.
Te recomendamos: Darles larga vida a los productos: una acción de sustentabilidad de PepsiCo México
Tiempo promedio del reabastecimiento de inventario
El primer paso, ya implica establecer con claridad si el porcentaje deseado de cobertura es viable de mantener.
El segundo elemento es el cálculo de la desviación media absoluta (Mean Absolute Deviation o MAD), es decir la variabilidad absoluta de la demanda del producto. Los registros que soportarían este cálculo, necesitan una certeza indiscutible, es decir, que la obtención de los mismos sea de una confiabilidad muy alta.
Aquí el método o protocolo de registro es la actividad clave y donde el empleo de la tecnología de la información cumple un rol de primer orden.
Finalmente, llegaríamos a el tiempo promedio de reabastecimiento (Lead Time o LT), que posea la historia del producto. Una vez calculado el nivel de seguridad o SS, entonces se calcularía el punto de reorden, siguiendo la fórmula que se despliega en la Figura 2.
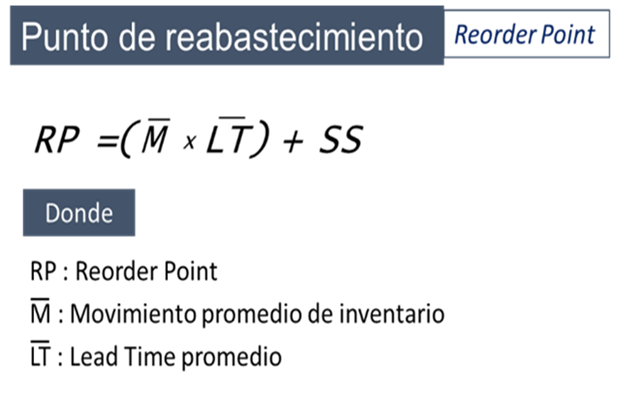
¿Qué niveles de inventario manejar?
Este punto de reabastecimiento, informaría sobre el nivel de inventario que accionaría el proceso de reabastecimiento.
¿En cuánta cantidad? En la necesaria para evitar exceder el máximo necesario, en el caso de los alimentos, debe cumplir con los preceptos que se tomaron en cuenta previo a la determinación del nivel mínimo o SS. Ahora bien, ¿cómo podríamos estimar el nivel máximo?
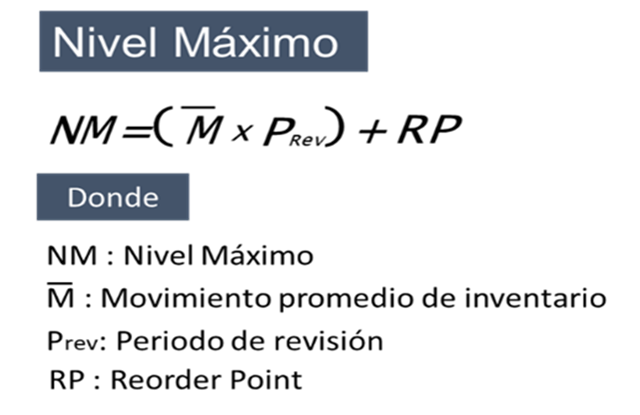
Al utilizar la formula tendríamos un estimado máximo que al sustraerle el mínimo (SS) nos daría el tamaño o cantidad de reorden sugerida.
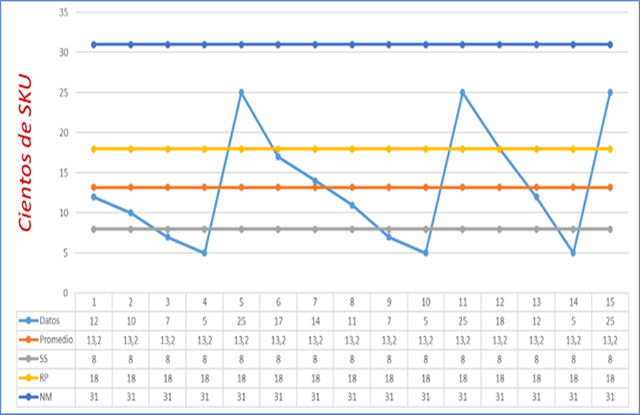
Con esta base es menester que los encargados de la gestión de los inventarios y la administración de los almacenes o ubicaciones de almacenamiento, parcial, temporal o por estación, puedan calcular, al menos empíricamente, los niveles de inventario que han de manejar.
Finalmente, la gran ventaja de lo anterior, es que se puede adaptar a la organización, los productos y procesos que maneja. Y muy especialmente, son la base de estructuración de modelos que a través de la tecnología de la información permitirán un mejor control tanto de costos como de las actividades asociadas.